News
SVOLT: The Future of Energy Storage Lithium Batteries is in Stacking - Witness the Golden Combination of Short Blades and Flying Stacks
On September 12, Yang Hongxin, Chairman and CEO of SVOLT, provided a first-person view of SVOLT's energy storage production base at the Chengdu plant, while publicly disclosing for the first time why the company has chosen a "non-standard" path for its energy storage products. He also explained why the L500 short-blade energy storage cells have gained recognition from leading domestic and international energy storage integrators and owners, and why the future of energy storage is in stacking, with stacking itself evolving through thermal composite processes.
"Three Generations Together": Chengdu Base Hosts Three Generations of Short-Blade Energy Storage Cells
During the factory tour, Yang introduced the three generations of short-blade energy storage cells that have already been deployed at SVOLT's Chengdu base.
The first generation is a 325Ah lithium iron phosphate short-blade stacking product with a cycle life exceeding 12,000 cycles. The second generation short-blade stacked energy storage cell features higher energy density, lower cost, and a capacity of 350Ah, enabling a 20-foot energy storage container to achieve a massive 6.9MWh capacity. Meanwhile, the company has also developed a third-generation energy storage cell—the 770Ah ultra-high capacity cell, which is set to enter mass production at the Chengdu base in the second quarter of 2025.
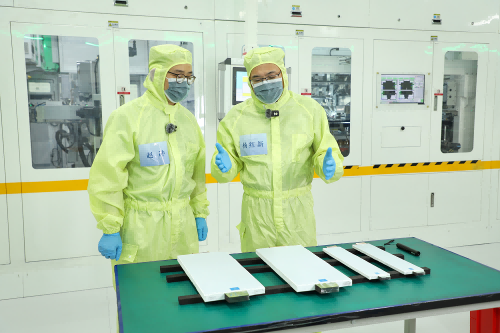
SVOLT has planned all three generations of its products in one go, all utilizing the company's industry-first third-generation thermal composite stacking technology. This approach offers significant advantages in terms of energy density, safety, and cycle life.
Currently, SVOLT’s L500 short-blade energy storage cells, with a capacity of 325Ah, have been integrated into GCL Group's "Xinyu+" large-scale storage products, enabling a 20-foot standard energy storage container to achieve a storage capacity of 6MWh. Recently, CRRC Zhuzhou Institute and SVOLT signed a collaboration agreement on ultra-high-capacity energy storage cells. In the future, SVOLT will provide the next-generation ultra-high-capacity stacked energy storage cells for CRRC Zhuzhou Institute's CESS-4.0 energy storage system.
Process Innovation: Thermal Composite Stacking as the Optimal Solution for Energy Storage Cells
"When a great product is developed, the key is how to manufacture it with high quality."
To ensure the quality of its batteries, SVOLT's Chengdu plant, which produces the 350Ah energy storage cells, is designed according to lighthouse factory standards, featuring a high degree of intelligence, automation, and unmanned operations. The automation rate of the entire production line exceeds 95%.
During the factory visit, Yang Hongxin explained that SVOLT's energy storage factory has achieved fully unmanned production, utilizing a multi-process integration method, which is the first in the industry to achieve simplified production. "The benefits are lower investment costs, lower energy consumption, and correspondingly lower manufacturing costs. Additionally, process integration reduces the number of times the cell electrodes are moved during production, resulting in higher product quality and safety."
At the site, it was evident that the loading and unloading during the coating process was fully automated using AGVs (Automated Guided Vehicles), significantly improving transportation efficiency and ensuring no manual contact throughout the process, making the electrodes safer. The production line also uses CCD (Charge-Coupled Device) online monitoring for real-time monitoring of coating speed and surface density, ensuring that every electrode meets quality standards 24 hours a day.
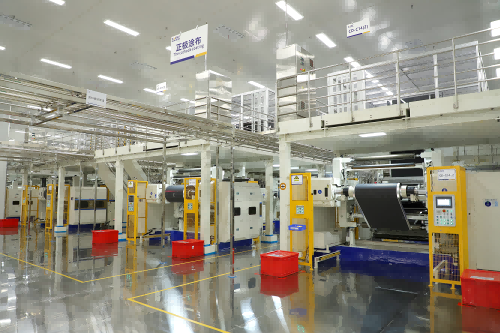
SVOLT's energy storage battery production line has introduced 832 CCD cameras for full-process defect detection, with over 1,200 quality control points. This ensures 100% defect detection during production, preventing any defective products from leaving the factory.
In the critical stacking process, SVOLT has implemented the world's first thermal composite flying stacking technology.
The thermal composite process involves bonding the separator and negative electrode together, solving issues like dusting and wrinkling commonly found in traditional stacking methods. The electrode surface after thermal composite stacking is extremely smooth and flat, eliminating the need for adhesive tape.
SVOLT's thermal composite flying stacking technology is an evolution of the successful application of this method in short-blade power batteries. It addresses the long-standing problems of slow stacking efficiency and low yield. In terms of core parameters such as safety, long lifespan, and fast charging, this technology not only outperforms winding methods but also demonstrates significant advantages over other stacking technologies in the industry.
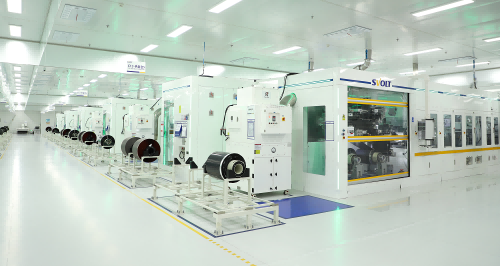
After years of exploration, technological breakthroughs, large-scale production validation, and market feedback, SVOLT firmly believes that the future of stacking lies in thermal composite stacking.
Breaking Tradition: Short-Blade Energy Storage Cells as the Optimal Solution for 20-Foot Energy Storage Containers
Currently, the mainstream energy storage cells on the market are based on the 71*173 mm size specifications of 280Ah or 314Ah cells, originally adapted from commercial vehicles. Most energy storage cell companies are still iterating their products based on this size.
"We went through intense internal debates and assessments before deciding to choose a path that is correct, but potentially difficult," said Yang Hongxin. SVOLT started from the underlying logic of energy storage systems and application scenarios, engaging in forward-looking development and design. The company believes that the energy storage cells of the future must meet the needs for safer system integration, higher module efficiency, and the potential for continuous iteration and upgrades.
Based on this, SVOLT, considering factors such as safety, system integration, modular efficiency, and cost reduction, concluded that the 500mm long, 215mm high L500 short-blade energy storage cell, utilizing stacking technology, is the optimal solution for 20-foot energy storage containers.
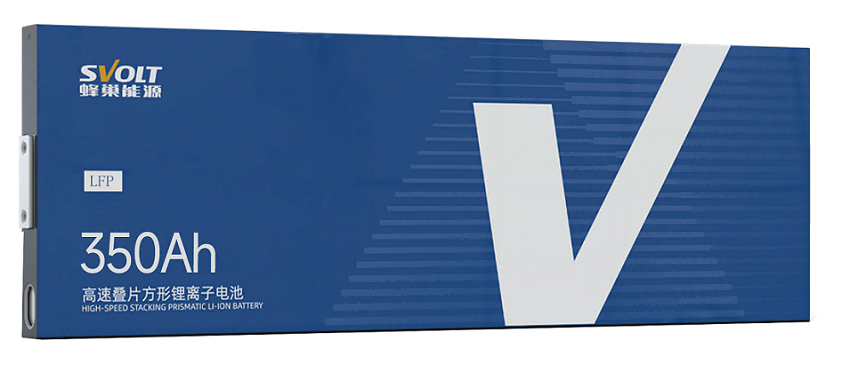
As a product developed specifically for energy storage applications, SVOLT’s L500 short-blade energy storage cell offers advantages in cost, safety, and performance compared to mainstream energy storage cells, and can create additional value for users.
Cost EfficiencyThe 350Ah L500 short-blade energy storage cell enables a 20-foot container to achieve a capacity of 6.9MWh, compared to the current mainstream 5MWh containers. This reduces system costs by 5% and decreases the required footprint by 28%, lowering both the initial acquisition cost and the levelized cost of energy (LCOE) over the system's lifecycle.
SafetyIn traditional winding processes, managing longer electrodes presents challenges in terms of winding speed and tension control, while uneven stress during discharge can lead to safety issues such as lithium plating on the negative electrode. These challenges, like wrinkling of electrode sheets, do not exist in stacking technology. The L500 short-blade cell, using stacking technology, eliminates these risks, offering a safer alternative.
PerformanceBesides safety, cycle life has become a key factor in the competition for energy storage cell performance, as it determines the total energy throughput over a project's lifecycle. SVOLT's stacking process has several advantages. First, each layer has its own tab, resulting in lower internal resistance compared to wound cells. Second, the L-shaped short-blade cell is thin, and heat dissipation through dual tabs on either side is efficient, leading to lower temperature rise and more uniform temperature distribution. Additionally, the L-shaped design generates less heat, improving the cell's cycle life.
On the system side, the L500 short-blade energy storage cell allows for dual-layer liquid cooling, reducing internal temperature differences by 8°C and increasing cycle life by 10% compared to traditional 71*173mm cells. Notably, the unique sealing design of the thermal composite process allows the cell to store an additional 2% of electrolyte, further extending its cycle life.
Advantages of Stacking and Thermal Composite Technology Thanks to the stacking process and thermal composite technology, SVOLT's energy storage cells offer excellent cycle life and safety performance. A longer cycle life means greater energy throughput over the system's lifecycle, creating more revenue for users.
The logic behind energy storage cells is to "scale up." The larger the cell, the lower the cost, and the higher the system integration efficiency. Stacking technology has inherent advantages in the development of energy storage cells. As a global leader in stacking technology, SVOLT has pioneered thermal composite technology and continues to drive the evolution of large-capacity cells. This has earned high recognition from top industry integrators. As mass production of these energy storage cells ramps up, SVOLT is expected to rapidly increase its market share in the global energy storage sector.
- Next:CATL: Building "Zero-Carbon New Infrastructure" to Co-create New Opportunities for Climate Action
- Previous:EVE Energy Showcases Innovation at Intersolar Summit Africa 2025
Contact Details
Lithium LiFePO4 Batteries and Lithium LiFePO4 Cells Supplier - LiFePO4 Battery Shop
Contact Person: Miss. Elena Wang
WhatsApp : +8615263269227
Skype : +8615263269227
WeChat : 15263269227
Email : info@lifepo4batteryshop.com
All Products
Certification
Customer Reviews
- I have fond memories of our meeting in Shanghai with LiFePO4 Battery Shop Elena. Your company left a strong impression on me with its impressive growth and professionalism. We both value straightforwardness and honesty, which I believe are the most important qualities in any partnership. I am confident that we can build a successful collaboration based on these shared values. —— Robert from USA
- I've been working with LiFePO4 Battery Shop for years, and their reliability is unmatched. While other suppliers frequently change sales teams, LiFePO4 Battery Shop has consistently provided exceptional service with a stable team. Their commitment to quality and customer support truly sets them apart. —— Henry from Australia