Blog
Understanding LiFePO4 Battery Cell Grading
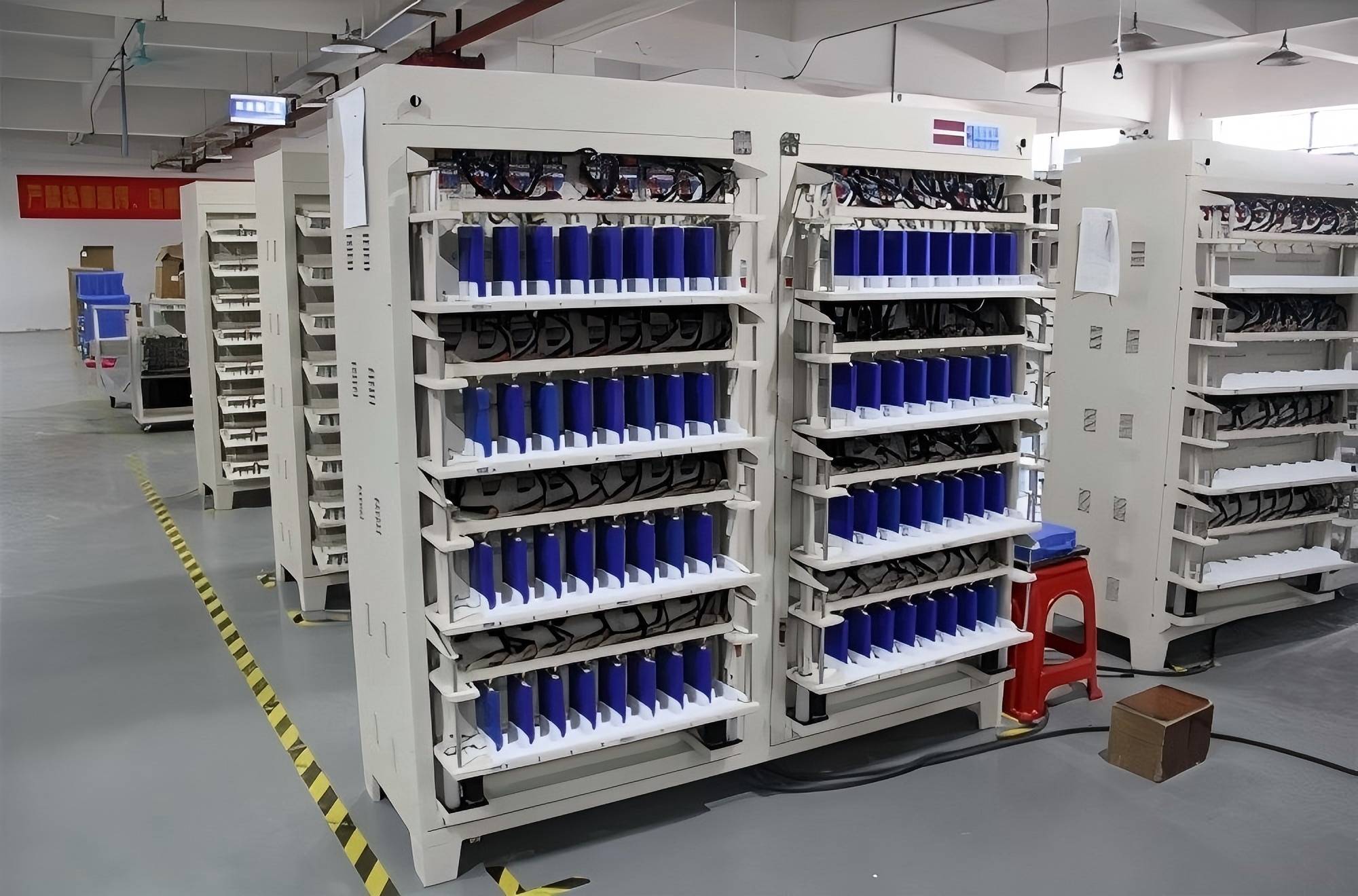
Lithium Iron Phosphate cell (LiFePO4 cell) grading is a critical process in the manufacturing of lithium-ion batteries, where cells are categorized based on key performance indicators such as capacity, voltage, and internal resistance. This ensures that only the highest-quality cells are used in the final battery assembly, leading to better overall performance and reliability.
In this article, we'll break down the concept of LiFePO4 cell grading, explain why it matters, and walk you through the steps involved in grading these cells to ensure consistency and optimal quality.
Why is LiFePO4 Cell Grading Important?
LiFePO4 cell grading plays a crucial role in ensuring the consistency of battery performance. Battery cells, even those with the same physical dimensions, can differ significantly in terms of their capacity and efficiency. Without proper grading, the end product could suffer from reduced performance or shorter lifespans. By grading the cells, manufacturers ensure that only those that meet the required standards are used, resulting in more reliable and efficient battery packs.
Understanding the Two Main Approaches to Cell Grading
There are two primary methods used for LiFePO4 cell grading, each focused on different aspects of battery performance.
1. Data Collection and Initial Analysis
During the first phase of the grading process, data is gathered from various points on the battery. This includes measurements of its voltage, internal resistance, and discharge capacity. A computer management system records this data and analyzes it to assess the battery's overall performance. The analysis determines the cell's capacity and internal resistance, which are key indicators of its quality.
After the initial grading, the cells are left to rest for at least 15 days. This period is essential because it allows any potential issues to surface. Batteries may appear to function well initially but could show signs of degradation or instability over time. The 15-day waiting period helps identify these hidden defects.
2. Capacity Testing for Quality Control
The second grading method focuses on testing the battery’s capacity. Despite having similar physical dimensions, lithium-ion cells can vary in their charge capacity. To test this, the cells are charged according to specific guidelines and then discharged at a designated current rate. The discharge time, when multiplied by the current rate, determines the cell’s capacity.
Cells that meet or exceed the required capacity are considered qualified, while those that fall short are rejected. This process ensures that only cells with sufficient capacity are used, contributing to the overall reliability of the battery pack.
The Role of Cell Formation
Cell formation is an important process that stabilizes the performance of a battery during its initial charge. It involves charging and discharging the cell at a low current rate and ensuring that it stabilizes at a consistent temperature. This process helps to eliminate initial performance issues and allows the battery to reach its optimal state before it’s used in any product.
How Cell Grading is Performed
The cell grading process is carried out using specialized equipment known as formation and grading cabinets. These cabinets are designed to simultaneously charge and discharge multiple cells while collecting data from each battery. The information gathered during this process is then analyzed to assess the capacity and internal resistance of each cell.
By using automated systems for grading, manufacturers can ensure that the cells are consistently tested under the same conditions, improving the accuracy of the results.
Post-Grading Storage and Re-testing
After the initial grading process, the batteries are stored for a minimum of 15 days. This period is crucial for detecting any potential issues that may not have been apparent during the initial grading phase. After the waiting period, the cells are re-tested to ensure that their capacity remains consistent and they still meet the required performance standards. Any cells that fail the re-test are removed from production.
This additional quality check ensures that the batteries are free from defects and ready for use in various applications, whether it's for electric vehicles, renewable energy storage systems, or consumer electronics.
The Benefits of LiFePO4 Cell Grading
The primary benefit of cell grading is the assurance of quality and consistency in battery packs. By carefully screening and sorting cells based on their performance, manufacturers can create battery packs that are more reliable, efficient, and longer-lasting. In addition, grading helps to minimize the risk of failure, improving the overall lifespan of the product.
Contact Details
Lithium LiFePO4 Batteries and Lithium LiFePO4 Cells Supplier - LiFePO4 Battery Shop
Contact Person: Miss. Elena Wang
WhatsApp : +8615263269227
Skype : +8615263269227
WeChat : 15263269227
Email : info@lifepo4batteryshop.com
All Products
- Sodium ion Battery Cell (0)
- Ternary Lithium Battery Cell (0)
- Battery Management System (0)
- Lithium Titanate Battery (4)
- Hybrid Inverter (6)
- CALB Battery (16)
- REPT Battery (7)
- Sinopoly Battery (7)
- A123 Battery (3)
- GBS Battery (16)
- CATL Battery (14)
- Thunder Sky Winston Battery (20)
- EVE Battery (19)
- LiFePO4 Battery Cell (4)
Certification
Customer Reviews
- I have fond memories of our meeting in Shanghai with LiFePO4 Battery Shop Elena. Your company left a strong impression on me with its impressive growth and professionalism. We both value straightforwardness and honesty, which I believe are the most important qualities in any partnership. I am confident that we can build a successful collaboration based on these shared values. —— Robert from USA
- I've been working with LiFePO4 Battery Shop for years, and their reliability is unmatched. While other suppliers frequently change sales teams, LiFePO4 Battery Shop has consistently provided exceptional service with a stable team. Their commitment to quality and customer support truly sets them apart. —— Henry from Australia